Troubleshooting
What do I do when a valve won't shut off?
There are steps that can be taken to troubleshoot this valve issue.
What if water comes out at the beginning of the system but not at the end?
There's a good chance your system demands more water than your line can carry. Another symptom of this is that you find that some watering devices throughout the system drip but some do not. You will need to add the total flow rates of the water dispensing devices on the line. For example, 10, 1 GPH emitters would use 10 GPH
1/2" line can carry a max of 240 GPH
3/4" line can carry a max of 480 GPH
1" line can carry a max of 780 GPH
Another important thing you must do is do a flow test to see how many GPH you have available at your water source. You can do this by doing a simple test at your spigot with a bucket and a stop watch. Instructions are in the link below.
https://www.dripworks.com/resources/calculators/flow-estimator
Once you know how many GPH your water source has, that info will assist in calculating how many drip devices you can use at once and what mainline tubing size may be most appropriate.
As an example, if you did the flow test and found that you had 300 GPH available, that means that you can max out a 1/2" mainline (240 GPH), or partially fill a 3/4" mainline (480 GPH).
Despite the fact that you have 300 GPH, if you use a 1/2" mainline, your flow budget for the system would be restricted to 240 GPH.
If you used a 3/4" line, since you don’t have the full 480 GPH needed to fill that line completely, your flow budget would be restricted to the 300 GPH that you have available.
As an example, if you calculate that in total on your system you have 600, 1 GPH emitters installed, that would mean that the system demands 600 GPH in order to operate correctly. If you had that amount of emitters on a 1/2" line, then only 240 GPH out of the 600 GPH needed would be met, causing malfunctions to the system.
If you used a 3/4" line, with a 300 GPH flow rate from the water source, only 300 GPH out of the 600 GPH needed would be met. You would need to split the system into two watering zones, and water one zone at a time. The system’s flow needs could be met if you set up the system with 2, 3/4" mainline zones, and only ran 300, 1 GPH emitters at one time on a zone.
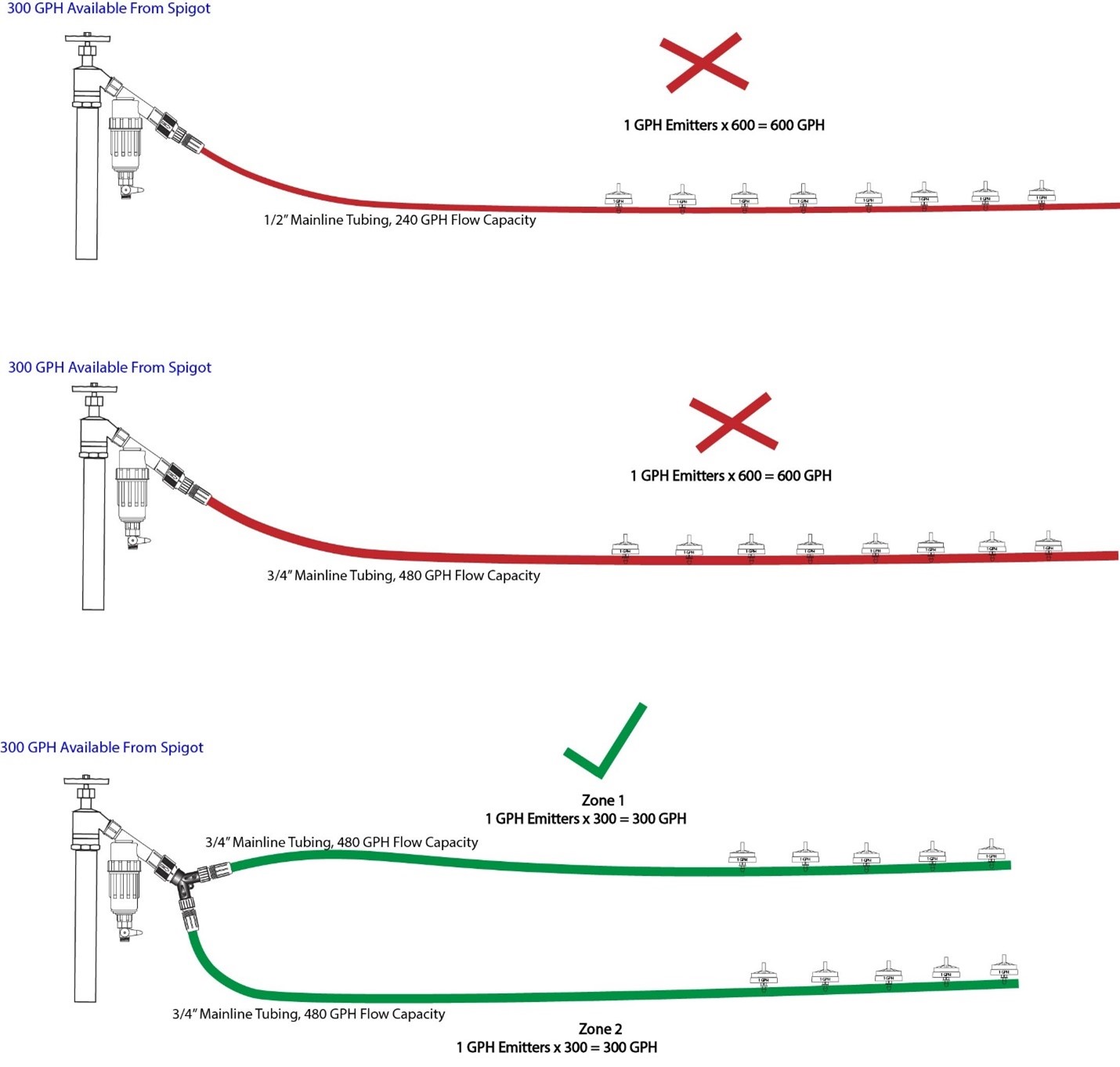
What if water is leaking from the body of my filter?
Open the filter by unscrewing the center of the body, remove the O-ring, and clean it, the groove it sits in and the surface it mates against. Re-assemble the filter and put it back in service. If the leak persists, replace the O-ring or see whether there is another source for the leak.
What could be wrong if less and less water is coming out of my system?
If a filter is present on the system, the screen inside of it may be dirty. As the screen catches debris from the water source, it creates a blockage, stopping the flow and pressure from the water source. You can take apart the filter body to remove the screen inside, once that is done, clean the screen by scrubbing it with a soft brush and rinsing it. Once it is cleaned of debris you can replace it back in the filter body and reinstall it. If there is no filter present in the system, your drip devices may be clogged from debris present in the water source being distributed throughout the system.
What could be wrong if emitters and fittings won't hold tight and keep coming off?
Likely, your pressure is too high. We suggest installing a pressure regulator after the filter.
I had a leaky emitter which I replaced with a goof plug, but it still leaks. How do I fix this?
First try a two-sided goof plug (14GP2) which has a standard sized plug on one end and an oversized plug on the other. If the hole still leaks you will need to cut out the leaky portion and insert a coupler that matches your size tubing.
I've connected my hose-thread device to my hose bib and it leaks like a sieve at the swivel. How can I make it stop?
Hose thread joints use round hose washers, placed in the female side of the connection. Check: Is the washer present? Is it cracked, worn out, or deformed? Is it evenly installed? If there is any question about its reliability replace it (HWASH) and treat with silicon lube (HLUBE) to prolong the life of and help make a water-tight connection. Check: If the male threads are too short when threaded into the female hose fitting to seat against the hose washer, the fitting will leak. Not all parts are manufactured to the exact same specifications, so lengths of male fittings and female sockets are not always consistent or compatible. Make sure there is a bit of space between the outside shoulders of the male/female connection. Check: Make sure the connection is hand tight but not TOO tight. Over tightening can cause a leak. Check: Make sure you haven't mixed threads. Pipe and Hose threads are incompatible. Connecting unlike threads can cause leaks, permanently deform the fittings, and result in serious issues down the road.
What do I do about leaks?
Leaks happen in a variety of ways for a variety of reasons. But the vast majority occurs at the threads. Check: How are the pipes/tubing joined? Are they hose thread by hose thread? Pipe thread by pipe thread? Hose thread by pipe thread? To stop hose thread leaks, lubricate the washer or O-ring with HLUBE) and hand tighten. If the leak persists, it might be time for a new washer/O-ring. Worst-case: the fitting has failed, but this is rare.
Why is my MixRite injector drawing fertilizer and clicking at a slower rate than it used to?
These symptoms indicate the seals are wearing out. You can replace your seals with the extra seals that came with your injector, or you can purchase a replacement seal kit.
My MixRite injector used to draw fertilizer but has recently stopped. What could be wrong? Why has my MixRite stopped drawing fertilizer?
Check that the washer at the top of the suction tube is in place and has a tight seal. Look to see that the check valve, just above the suction assembly, is not clogged with debris, moves freely, and is able to fully close. Make sure the screen at the bottom of the suction tube is clear of debris as well.
Why is my pressure regulator weeping?
A normally operating pressure regulator or limit valve will weep occasionally as a normal response to hydrodynamic variations.
Why does my battery timer come on but not shut off?
Timers with a diaphragm need a minimum flow and pressure to operate correctly, usually 30 gph and 15 psi. Water surge on start-up can "fool" the timer into opening but once the initial flow and pressure drop, it will not close when scheduled. To test this, open the end of your mainline and, if the timer shuts off when it is supposed to, you know you do not have enough water flowing through your system. If you have several small zones, you might consider consolidation to fewer, larger zones to increase flow. Battery timers can also use a lot of power to open and close the valve inside, be sure that your battery is fresh and is an industrial strength alkaline battery.
Why won't my Galcon High Flow timer shut off like it used to?
The Galcon High Flow timer (TGNHF) has a manual on/off "switch", a yellow/orange handle on the downstream side of the timer. If the timer will not shut-off it may mean that this handle was turned. Turn it back and check to see if the water stops flowing. This should return the timer to its normal programming. If it still does not operate correctly, it could relate to debris blocking the valve or other problems.
*Note: debris in ANY valve or timer can cause operating issues and is not covered by warranty
Why is it that my water meter reads high usage while the water level in my tank seems to remain about the same and my crops do not seem to be getting enough water?
If the water meter is showing flow, it can be either water or air. Air can travel at 29 times the velocity of water and a water meter does not distinguish the difference between the two. If there is relatively little water loss but the meter continues to register usage, you may need to place an air bleed valve at a high point before the meter to eliminate trapped air.
My battery timer worked fine at first but now water barely trickles out. Could dirty water be the cause?
Yes. It sounds like the hose washer screen is clogged with debris. Be sure to clean the screen frequently or, better yet, install a larger, constant pressure filter before the timer to ensure it stays clean.
I turn on my EZ-Flo injection system and no fertilizer seems to be coming out while water is coming in. What should I do?
If there is no fertilizer flowing after a few minutes of operation, shut off the system, wait a few moments and restart it. When starting, the system water flows into the tank until it is totally full and at the same pressure as the watering system. Fertilizer will begin to flow once this has happened. This can take a minute or more when the tank is refilling. Remember, the tank must be completely full of fluid before fertilizer starts to flow. Fertilizer with dark dye coloring will look darker flowing through the clear tubing than lighter colored fertilizers, even though they are feeding at the same rate. With low flow systems the fertilizer flowing through the tubing may have less color because the system automatically adjusts the fertilizer ratio to the water going through the system. Dry fertilizers can take longer to begin flowing than liquid fertilizers because they need to dissolve first. If you are using tubing valves, make sure they are in the "on" position. The green fitting on the cap is connected to the clear, downstream tube, while the blue fitting on the cap is connected to the black, upstream tubing.
Why are my emitters not dripping?
A common thing to happen is that the emitters were installed upside down. If you are using emitters that are color coded for flow rate, such as the woodpecker emitters or CETA PC emitters, be sure that the colored side is facing down towards the tubing that it is installed into.
I installed a pressure gauge after my pressure regulator and it appears that the regulator is not reducing the PSI, what could be wrong?
Pressure regulators begin reducing the PSI once the minimum flow requirement has been met, so there needs to be enough flow running through the system for the regulator to work correctly. If you install a hose after the pressure regulator, and then test the pressure at the end of the hose, you will begin to see the pressure reduction. Regulators such as our Lawn and Garden pressure regulator (Item PRSG) needs a minimum of 0.5 GPM (30 GPH) running through the system in order for it to begin reducing the pressure to the chosen amount (either 10, 20, 30, or 40 PSI).
I have both sediment debris and algae coming from my water source, what can I do to keep my system from clogging?
In this scenario, installing a disc filter first, followed by a screen filter should be enough to catch all debris types. Both disc and screen filters are available in large sizes also, the larger the filter area, the less time between cleaning out the filters.